How to Identify What is Porosity in Welding and Improve Your Strategy
Wiki Article
The Science Behind Porosity: A Comprehensive Overview for Welders and Fabricators
Comprehending the elaborate mechanisms behind porosity in welding is important for welders and fabricators striving for flawless craftsmanship. From the structure of the base products to the details of the welding process itself, a wide variety of variables conspire to either aggravate or relieve the existence of porosity.Comprehending Porosity in Welding
FIRST SENTENCE:
Examination of porosity in welding reveals important understandings into the honesty and quality of the weld joint. Porosity, characterized by the visibility of dental caries or gaps within the weld steel, is an usual worry in welding processes. These gaps, if not correctly resolved, can endanger the architectural integrity and mechanical homes of the weld, bring about potential failures in the completed product.
To find and evaluate porosity, non-destructive testing techniques such as ultrasonic screening or X-ray assessment are usually used. These strategies permit the recognition of interior problems without compromising the honesty of the weld. By analyzing the dimension, form, and distribution of porosity within a weld, welders can make educated choices to boost their welding processes and attain sounder weld joints.
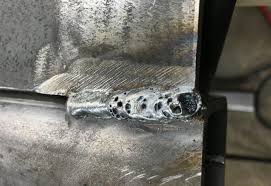
Variables Influencing Porosity Development
The event of porosity in welding is affected by a myriad of factors, ranging from gas protecting efficiency to the details of welding parameter setups. Welding specifications, consisting of voltage, existing, take a trip speed, and electrode kind, likewise impact porosity formation. The welding technique used, such as gas steel arc welding (GMAW) or secured metal arc welding (SMAW), can influence porosity formation due to variations in warmth circulation and gas insurance coverage - What is Porosity.Impacts of Porosity on Weld Top Quality
The visibility of porosity also weakens the weld's resistance to corrosion, as the entraped air or gases within the gaps can react with the surrounding setting, leading to deterioration over time. Additionally, porosity can prevent the weld's capability to stand up to stress or effect, additional jeopardizing the general top quality and reliability of the bonded structure. In critical applications such as aerospace, vehicle, or structural building and constructions, where safety and security and longevity are paramount, the harmful impacts of porosity on weld top quality can have serious effects, stressing the importance of minimizing porosity through proper welding methods and procedures.home
Techniques to Decrease Porosity
Furthermore, using the appropriate welding specifications, such as the right voltage, present, and travel speed, is important in avoiding porosity. Keeping a consistent arc size and angle during welding additionally helps reduce the chance of porosity.
In addition, choosing the ideal securing pop over here gas and preserving appropriate gas circulation rates are important in lessening porosity. Making use of the appropriate welding strategy, such as back-stepping or employing a weaving activity, can additionally assist disperse warmth evenly and reduce the chances of porosity development. Last but not least, ensuring appropriate air flow in the welding setting to eliminate any kind of prospective resources of contamination is important for attaining porosity-free welds. By carrying out these methods, welders can successfully minimize porosity and generate top quality welded joints.
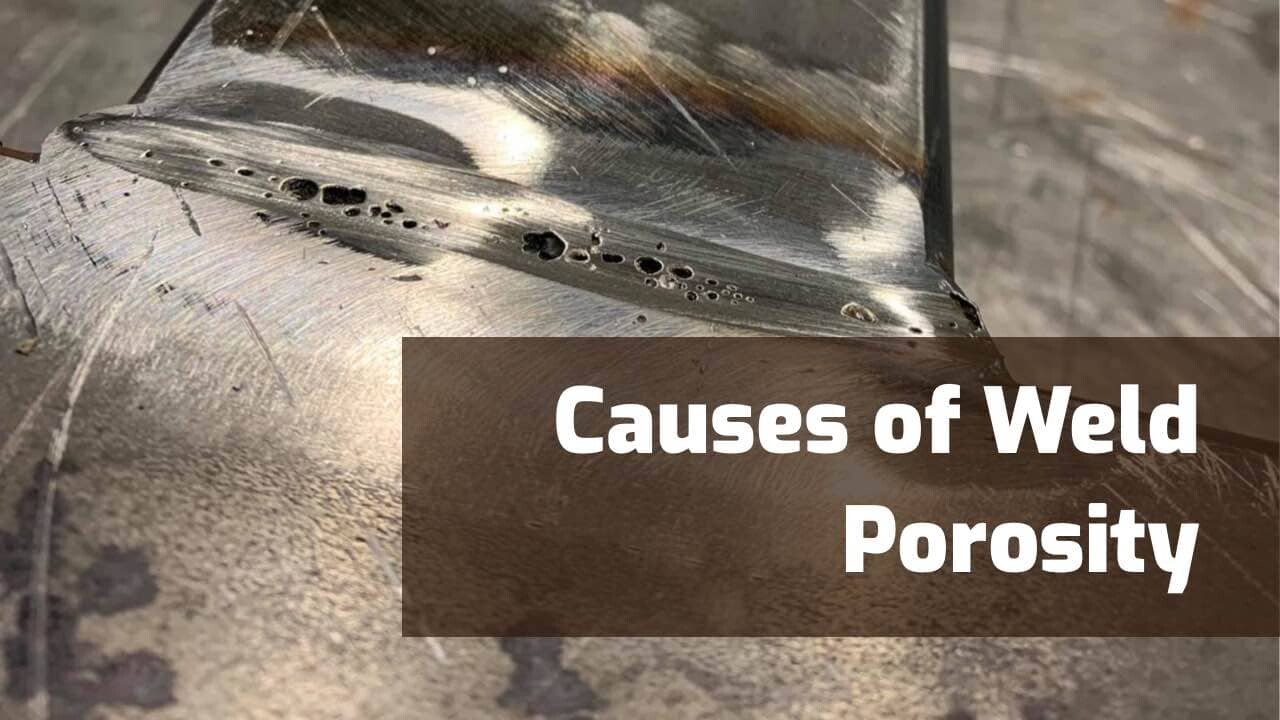
Advanced Solutions for Porosity Control
Implementing innovative modern technologies and cutting-edge techniques plays a pivotal function in achieving exceptional control over porosity in welding procedures. In addition, employing advanced welding methods such as pulsed MIG welding or customized ambience welding can additionally aid mitigate porosity concerns.An additional innovative remedy involves using advanced welding equipment. For example, making use of devices with integrated attributes like waveform control and advanced power sources can improve weld quality and decrease porosity dangers. Additionally, the implementation of automated welding systems with exact control over specifications can significantly reduce porosity issues.
Furthermore, integrating sophisticated monitoring and evaluation modern technologies such as real-time X-ray imaging or automated ultrasonic testing can help in discovering porosity early Continued in the welding process, enabling for prompt rehabilitative activities. Overall, incorporating these innovative remedies can significantly improve porosity control and enhance the overall top quality of bonded components.
Conclusion
Finally, comprehending the science behind porosity in welding is essential for welders and makers to create high-grade welds. By determining the factors influencing porosity formation and implementing strategies to reduce it, welders can boost the general weld quality. Advanced solutions for porosity control can additionally improve the welding process and guarantee a strong and trustworthy weld. It is very important for welders to constantly enlighten themselves on porosity and implement best practices to attain optimum results.Report this wiki page